What Are Examples of Successful Cost-Reduction Strategies in Manufacturing?
From the strategic perspective of a Supply Chain Manager, we explore effective cost-reduction strategies that have been successfully executed in the business world. Alongside expert insights, we've gathered additional answers that delve into a range of tactics, from adopting lean manufacturing principles to implementing just-in-time inventory systems. Here's a closer look at seven proven strategies that can help companies streamline operations and save costs.
- Eliminate Waste in Supply Chain
- Optimize Procurement Processes
- Adopt Lean Manufacturing Principles
- Upgrade to Energy-Efficient Technology
- Outsource Ancillary Processes
- Invest in Automation Technology
- Implement Just-In-Time Inventory
Eliminate Waste in Supply Chain
There are many ways to reduce costs. The key is to eliminate waste. In production, this could be through line balancing, i.e., each station takes the same amount of processing time; therefore, the total production time is minimal and efficient. In component parts, make sure defects are minimal—eliminate finding component defects from the production line. In supplier costing, challenge the details of the pricing, i.e., labor rates, FX, cost of raw materials, processing time, profit, SG&A, any add-ons, etc. With inventory management, forecasting is key to good planning and managing inventory; too much or too little inventory is very costly to a company. A well-executed forecast can prevent inventory from sitting in a warehouse or angry customers waiting for their orders. Basically, look to areas in the supply chain that can be more efficient by eliminating waste. The successful strategy to cost reduction is the more efficient and balanced the supply chain, the better overall for the company to reduce costs.
Optimize Procurement Processes
One strategy we continuously apply in order to manage and reduce costs is focusing on our procurement. This means we have regular reviews and catch-ups with our suppliers to make sure that the existing agreements and relationships are still suitable for our growth. For example, as we have expanded and our volume has increased, the pricing we negotiated for raw materials at certain quantities no longer makes sense, as we are purchasing much more. By keeping on top of this, we can ensure the highest profit margins, prevent spending from being lost through being oblivious or negligent, and it also nurtures the inquisitive attitude of 'Is this still the right choice for us?' which is essential to success.
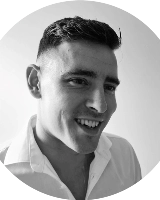
Adopt Lean Manufacturing Principles
Adopting lean manufacturing principles is a powerful way to reduce waste and improve efficiency. Lean strategies focus on streamlining operations, eliminating unnecessary steps, and ensuring that every action adds value to the end product. By concentrating on minimizing the use of resources and maximizing productivity, manufacturers can significantly lower costs.
This approach not only reduces expenses but also often leads to quicker production cycles and improved product quality. Manufacturers seeking to optimize their processes should consider implementing lean practices to enhance their competitive edge.
Upgrade to Energy-Efficient Technology
Implementing energy-efficient technologies is an effective strategy that can lead to significant cost savings over time. Upgrading to energy-saving equipment and systems can reduce power consumption, which is often one of the largest expenses for manufacturing facilities. This strategy has the added benefit of making the operation more environmentally friendly, which can also lead to tax incentives and a positive brand image.
Energy-efficient lighting, motors, and heating systems are examples of upgrades that can lead to a reduction in utility bills. Manufacturers keen on cutting costs and supporting sustainability should explore energy-efficient solutions.
Outsource Ancillary Processes
Outsourcing non-core activities allows a manufacturing business to focus on its primary expertise while ancillary processes are handled by specialists. By contracting out functions like transportation, maintenance, or even certain stages of production, companies can take advantage of the economies of scale and expertise offered by third-party providers. This reduces the need to invest in equipment and training for tasks that are outside the company’s main business function.
It also potentially lowers labor costs and liabilities. Companies aiming to be more streamlined should consider the benefits of task delegation to reliable outsourcing partners.
Invest in Automation Technology
Automating repetitive tasks can bring about a transformation in manufacturing by significantly reducing the time and labor required for production. Automation technology, such as robotics and AI, can perform routine jobs with greater precision and consistency than human workers. This not only improves the speed of production but also the quality, leading to fewer errors and less waste.
In the long term, investment in automation can offer substantial financial return by decreasing labor costs and increasing output. Manufacturers should assess the potential for automation to revolutionize their production lines.
Implement Just-In-Time Inventory
Utilizing just-in-time inventory systems is an innovative strategy to manage material flows and reduce the costs associated with excess inventory. Just-in-time practices involve scheduling materials to arrive exactly when they are needed for production, thereby minimizing storage costs and reducing the risk of waste from overstocking. This method requires precise planning and good relationships with suppliers to ensure timely delivery of components.
The efficiency gained from a well-executed just-in-time system can give manufacturers a significant financial advantage. To stay competitive and lean, manufacturers could benefit from examining their inventory management and considering a just-in-time approach.