How Do Manufacturing Engineers Tackle Complex Problems?
Manufacturing Engineers often face intricate challenges that require innovative solutions, as demonstrated by a Senior Welding Applications Engineer who employed a holistic approach to tackle weld failure. Alongside expert insights, we've gathered additional answers that highlight the diverse strategies used to resolve complex manufacturing problems. From the implementation of real-time monitoring systems to fostering teamwork across disciplines, discover how these professionals turn obstacles into successes.
- Holistic Approach to Weld Failure
- Introduce Automation for Efficiency
- Utilize Advanced Data Analytics
- Adopt Lean Manufacturing Principles
- Foster Multidisciplinary Team Collaboration
- Implement Real-Time Monitoring Systems
Holistic Approach to Weld Failure
Hello,
I’m the weld engineer at NS ARC and would love to share an instance in which I overcame a complex problem by utilizing a holistic approach to the situation:
In a recent consulting assignment, a critical piece of manufacturing equipment, out in the field, failed unexpectedly due to a weld issue. My task was to perform a deep analysis of this failure and determine the root cause, which required top precision, attention to detail, and a keen understanding of the complexities of the machine.
I began my investigation by sending samples of the failed part—a combination of a casting and steel components—to an external laboratory for careful chemical analysis and then meticulously matching casting specifications with component results. Employing both Ultrasonic Testing and X-ray techniques, the failed weld underwent cross-sectional analysis and etching. Additionally, I evaluated the welding parameters and the welding cell to ensure a thorough examination.
Through my analysis, I tracked the root cause back to plant shielding gas piping. Excessive demand from multiple welding stations caused a deficiency in shielding gas, starving the two welding cells in question that supported the manufacturing of the failed assembly. The stealthy lack of shielding gas directly affected weld penetration, leading to stress risers, cracks, and eventual failure during service.
In addressing this challenge, I was able to rectify the immediate welding parameters and optimize the shielding gas delivery system. This not only ensured the quality of the welds but also prevented similar failures from happening again. The outcome was not just a repaired piece of equipment but a fortified manufacturing process that can now stand resilient against future sudden challenges.
This experience really emphasized the importance of a holistic approach to problem-solving in manufacturing. A thorough and methodical investigation can link a seemingly isolated weld failure to larger systemic issues, giving you the chance to identify, address, and prevent further problems from occurring. It was a testament to the critical role that precision and attention to detail play in the field.
I hope my story helps your article. Please reach out to me if you have any questions. I am more than happy to provide anything you may need.
Best of luck with the article,
Nate Vanderhoof | Senior Welding Applications Engineer, North America
MBA, BSWET, AWS CWI #16012741 / CWE #1601010E
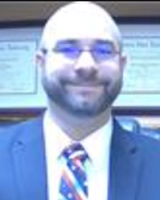
Introduce Automation for Efficiency
Manufacturing engineers often introduce cutting-edge automation technologies to streamline production processes. These technologies can range from robotics to advanced software that automates complex tasks, thus reducing the likelihood of human error and increasing efficiency on the production floor. With automation, they can ensure consistent quality and outputs, which is critical for meeting both customer expectations and industry standards.
By reimagining the production line through automation, they are adept at solving issues that otherwise would require labor-intensive solutions. Consider exploring how automation can enhance your manufacturing processes.
Utilize Advanced Data Analytics
The use of advanced data analytics tools by manufacturing engineers is pivotal in solving complex problems. By analyzing vast amounts of data, they can uncover patterns, predict failures, and improve processes that were not visible before. Data analytics allows for making informed decisions based on actual performance metrics and operational data.
This evidence-based approach to problem-solving ensures a reduction in trial and error and accelerates the identification of optimal solutions. Look into data analytics to refine your manufacturing operation's efficiency and problem-solving capabilities.
Adopt Lean Manufacturing Principles
Adopting lean manufacturing principles is a strategy manufacturing engineers use to address complex issues. Lean principles focus on reducing waste and optimizing processes, delivering value to customers while utilizing fewer resources. Emphasizing the importance of continuous improvement, engineers work to eliminate any steps that do not add value to the end product.
This lean approach encourages a culture of efficiency and can lead to remarkable improvements in quality and production speed. Investigate how lean manufacturing could transform your practices and elevate your business' productivity.
Foster Multidisciplinary Team Collaboration
Collaboration in multidisciplinary teams is another method manufacturing engineers use to tackle complex problems. By working together, experts from different fields such as engineering, finance, and operations can pool their knowledge to formulate well-rounded solutions. This collaborative approach not only ensures that multiple perspectives are considered, but it also fosters innovation and creativity in addressing challenges.
Ultimately, this diversity in thought can lead to more resilient and effective solutions. Encourage diverse collaboration in your workplace to gain a broader perspective on challenging issues.
Implement Real-Time Monitoring Systems
Finally, incorporating real-time monitoring systems is a technique used by manufacturing engineers to solve problems. These systems provide a continuous stream of data, allowing engineers to monitor operations and spot irregularities as they occur. With instant feedback, actions can be taken swiftly to correct any issues, thus preventing small problems from developing into major setbacks.
The real-time insight gained from these systems can be invaluable for maintaining a smooth and responsive manufacturing process. If efficiency and proactive problem solving are your aims, consider implementing real-time monitoring in your operations.