7 Successful Quality Control Systems Implemented in Manufacturing
Have you ever wondered how leading professionals elevate their operations with cutting-edge quality control systems? In this article, insights from an Owner and a Continuous Improvement Manager reveal transformative strategies. The first insight highlights a structured plant health assessment process, while the final takeaway focuses on supplier collaboration and quality management, among a total of seven expert insights. Uncover these key approaches that have significantly impacted their operational success.
- Structured Plant Health Assessment Process
- Three-Stage Quality Control Process
- Automation and Real-Time Monitoring
- Employee Training and Empowerment
- Continuous Improvement and Feedback Loops
- Data Analysis and Statistical Process Control
- Supplier Collaboration and Quality Management
Structured Plant Health Assessment Process
A standout example of a quality control system I implemented was the introduction of a structured plant health assessment process for every client visit. After years of experience and training as a certified horticulturist, I noticed that many common garden issues could be prevented with early detection, but they often went unnoticed until they became costly and labor intensive to address. I created a checklist system for my team to follow, focusing on signs of disease, pest presence, soil health, and overall plant vitality. This checklist is now a core part of our service, allowing us to consistently monitor the health of our clients' plants and proactively address issues before they escalate. I also made sure to train my team thoroughly on plant diagnostics, passing on the knowledge I built up over the years to ensure they understand what to look for in a quick and systematic way.
The impact on our operations has been significant. By catching issues early, we've reduced the need for emergency interventions by over 40 percent, allowing us to work more efficiently and keep client gardens healthier year-round. This approach has also built strong trust with clients, as they see the consistent care we provide and the expertise we bring to every job. It's been rewarding to see how my background in both practical gardening and horticultural theory directly supports this quality control process, ensuring we deliver high standards while also maintaining the beauty and longevity of each garden we care for.
Three-Stage Quality Control Process
Implementing any change can be challenging, and it's easy for people to feel overlooked or for communication to get lost along the way. To address this, we've introduced a three-stage quality control process with the KISS principle at its core; Keep It Simple and Sustainable. Here's how it works:
When a new idea for improvement arises, we bring it to the entire management team. Together, we discuss who needs to be involved to make the change effective. From there, we kick off with a PDCA (Plan - Do - Check - Act) cycle:
Plan - We clarify assignments, set realistic timelines, and ensure everyone is on the same page.
Do - The process is first tested on a small scale with a select group to see how it performs.
Check - We then hold a meeting to review what worked, what didn't, and any adjustments needed.
Act - With the lessons learned, we roll out the final process, ensuring everyone involved is trained and informed.
This approach has allowed us to move forward with confidence and clarity, confident everyone's voice is heard and each step is intentional. We're not just implementing change-we're building a foundation that's designed to last which is responsive to the needs of our organization vs being reactive.
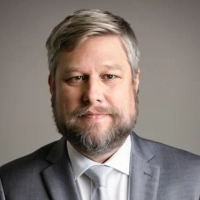
Automation and Real-Time Monitoring
Automation and real-time monitoring are crucial for successful quality control systems as they ensure that manufacturing processes are efficient and consistent. By implementing automated systems, manufacturers can reduce human errors and maintain high standards. Real-time monitoring allows for immediate detection and correction of any issues, minimizing waste and increasing productivity.
This approach not only improves the quality of the final product but also reduces costs associated with defects and rework. Invest in automation and monitoring solutions to enhance your manufacturing quality now.
Employee Training and Empowerment
Employee training and empowerment play a vital role in ensuring quality in manufacturing. When employees are well-trained, they are better equipped to identify and address potential quality issues. Empowering employees to take ownership of their work encourages them to maintain high standards and take pride in their contributions.
This leads to a culture of continuous improvement, where every team member is committed to delivering quality products. Focus on training and empowering your workforce to see impressive improvements in manufacturing quality.
Continuous Improvement and Feedback Loops
Continuous improvement and feedback loops are essential for maintaining high-quality standards in manufacturing. By constantly seeking ways to improve processes, manufacturers can adapt to changing demands and stay ahead of competitors. Feedback loops provide valuable insights into areas that need enhancement, allowing for timely and effective adjustments.
This iterative process ensures that quality is always being refined and optimized. Commit to continuous improvement and establish feedback loops to keep your manufacturing processes at their best.
Data Analysis and Statistical Process Control
Data analysis and statistical process control are key components of effective quality control systems in manufacturing. Utilizing data analysis techniques, manufacturers can identify trends, detect anomalies, and predict potential issues before they occur. Statistical process control helps in maintaining consistent quality by monitoring production processes and making necessary adjustments based on data-driven insights.
This proactive approach leads to better decision-making and a higher quality output. Implement data analysis and statistical process control to drive quality in your manufacturing operations.
Supplier Collaboration and Quality Management
Supplier collaboration and quality management are critical to ensuring the success of quality control systems in manufacturing. Collaborating closely with suppliers helps in setting clear quality expectations and ensuring that raw materials meet the required standards. Effective supplier quality management involves regular communication, audits, and performance reviews to maintain high standards throughout the supply chain.
This partnership approach ensures that quality is upheld from the very beginning of the production process. Foster strong relationships with your suppliers to enhance the quality of your manufacturing operations.