7 Strategies to Reduce Downtime and Improve Equipment Reliability
Downtime and equipment reliability are critical concerns for businesses across industries. This article presents expert-backed strategies to address these challenges head-on. From empowering employees to implementing cutting-edge technologies, discover practical approaches to enhance operational efficiency and minimize costly disruptions.
- Empower Employees to Report Equipment Issues
- Implement Predictive Maintenance for Early Detection
- Use Real-Time Monitoring to Prevent Failures
- Invest in Comprehensive Operator Training Programs
- Optimize Inventory Management for Critical Parts
- Develop Standardized Maintenance Procedures and Checklists
- Invest in Equipment Redundancy for Critical Systems
Empower Employees to Report Equipment Issues
Obviously, having a robust preventative maintenance program is the number one goal. However, if there are deficiencies in that process, it is important to empower your employees to speak up and stop the equipment when they notice the equipment is exhibiting different conditions than normal. The employee does not have to be a maintenance technician to notice problems as they occur - they can notice a change in the harmonics of a pump, the smell of a belt slipping, or the sight of oil drops on the floor (as examples). Empower employees to speak up and ensure early issues are addressed immediately to avoid more serious issues in the future.
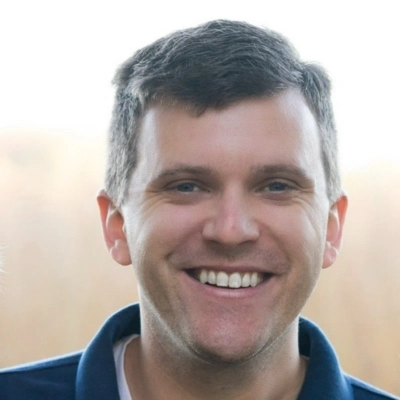
Implement Predictive Maintenance for Early Detection
In our manufacturing facility, we've focused heavily on predictive maintenance to reduce downtime and improve equipment reliability. This approach uses sensors and advanced analytics to monitor the condition and performance of machinery. By predicting when a piece of equipment is likely to fail or need maintenance, we can intervene beforehand, thereby preventing unplanned downtime and extending the equipment's life span. For example, by implementing vibration analysis on our conveyor systems, we've been able to detect unusual patterns that indicate wear and tear on bearings before they cause a malfunction.
One specific success was observed on one of our main production lines, which had faced frequent unexpected stoppages. After applying thermal imaging techniques along with vibration analysis, we preemptively identified and replaced several overheating motors and worn belts. As a result, the production line's downtime was cut by approximately 40% in the following quarter. This not only helped in maintaining the flow of operations but also reduced the stress on other machinery components, thus optimizing our overall maintenance costs. The takeaway here is that investing in predictive maintenance not only reduces disruptions but also contributes positively to the operational budget by saving costs related to emergency repairs and unplanned downtime.
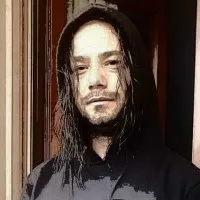
Use Real-Time Monitoring to Prevent Failures
Implementing real-time condition monitoring and predictive analytics can significantly reduce equipment downtime. By using sensors and data analysis, companies can detect potential issues before they cause failures. This proactive approach allows maintenance teams to schedule repairs during planned downtimes, minimizing disruptions to operations.
The collected data can also help identify patterns and optimize maintenance schedules. With these insights, businesses can extend the lifespan of their equipment and improve overall reliability. Start exploring real-time monitoring solutions to enhance your equipment management strategy.
Invest in Comprehensive Operator Training Programs
Establishing comprehensive operator training and certification programs is crucial for improving equipment reliability. Well-trained operators can better understand the machinery they work with, reducing the risk of human error. These programs should cover proper equipment operation, basic troubleshooting, and early problem detection.
By investing in employee knowledge, companies can create a culture of responsibility and care for equipment. This approach not only reduces downtime but also enhances workplace safety and job satisfaction. Consider implementing a structured training program to empower your operators and boost equipment performance.
Optimize Inventory Management for Critical Parts
Optimizing inventory management for critical spare parts is essential in minimizing equipment downtime. By maintaining an appropriate stock of crucial components, companies can quickly address unexpected breakdowns. Effective inventory management involves identifying critical parts, forecasting demand, and establishing reorder points.
This strategy helps balance the costs of storing spare parts with the potential losses from equipment downtime. Implementing a digital inventory system can further streamline this process, providing real-time visibility of available parts. Take steps to review and improve your spare parts management to ensure rapid response to maintenance needs.
Develop Standardized Maintenance Procedures and Checklists
Developing standardized maintenance procedures and checklists can greatly improve equipment reliability. These tools ensure that all necessary maintenance tasks are performed consistently and thoroughly. Standardized procedures help reduce variability in maintenance quality and make it easier to train new staff.
They also create a valuable knowledge base that can be updated and refined over time. By documenting best practices, companies can preserve institutional knowledge and continually improve their maintenance processes. Start creating detailed, step-by-step maintenance guides for your critical equipment to enhance consistency and efficiency.
Invest in Equipment Redundancy for Critical Systems
Investing in equipment redundancy for critical systems is a powerful strategy to minimize downtime. By having backup equipment ready, companies can quickly switch operations when primary systems fail. This approach is particularly important for processes where even short interruptions can cause significant losses.
While redundancy requires upfront costs, it can lead to substantial savings by preventing production stops and rush repair expenses. The key is to identify the most critical systems and prioritize redundancy investments accordingly. Evaluate your critical processes and consider implementing redundancy to safeguard against unexpected failures.