7 Challenges and Insights from Implementing Industry 4.0 Technologies
Diving into the realm of Industry 4.0 presents a unique set of challenges that beckon for expert insights. This article peels back the layers of complexity by sharing knowledge from seasoned professionals who've navigated the integration of cutting-edge technologies within established frameworks. Readers will gain practical strategies for adopting Industry 4.0, directly from those who've mastered its intricacies.
- Integrating Legacy Systems with New Technologies
- Phased Approach for IoT Retrofits
- Prioritize Data Security
- Train Workforce for New Technologies
- Manage Costs for Industry 4.0
- Address Interoperability Issues
- Monitor ROI for Industry 4.0
Integrating Legacy Systems with New Technologies
One key challenge I faced in implementing Industry 4.0 technologies in our manufacturing operations was the integration of legacy systems with new smart technologies. Our manufacturing processes were heavily reliant on older machinery and software that weren't initially designed to communicate with the more advanced sensors, robotics, and IoT devices we wanted to integrate. Bridging the gap between these systems required significant investment in upgrading or retrofitting equipment, as well as ensuring compatibility between the old and new systems.
One of the insights I gained was the importance of taking a phased, strategic approach to integration. Rather than trying to overhaul everything at once, we focused on implementing a few critical Industry 4.0 technologies-like predictive maintenance sensors and real-time data analytics-while gradually upgrading older equipment. This allowed us to minimize disruptions and test the effectiveness of each technology before scaling up.
I also learned that proper staff training is essential when integrating new technologies. Employees need to feel comfortable using and managing the new systems, so we invested in continuous training to ensure they could adapt to the evolving digital landscape.
Ultimately, while the integration process was complex, it significantly improved our operational efficiency and allowed us to gather real-time insights that helped optimize production and reduce downtime. The experience taught me that successful Industry 4.0 implementation requires careful planning, testing, and a gradual approach to ensure that all systems work harmoniously together.
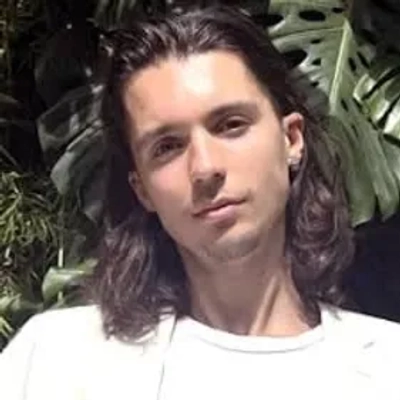
Phased Approach for IoT Retrofits
One major challenge our manufacturing clients face with Industry 4.0 is integrating new tech with legacy systems—old machines don't always play nice with smart sensors and AI-driven platforms. One client struggled with getting real-time data from decades-old equipment, leading to inconsistent insights. The fix? A phased approach—starting with IoT retrofits instead of full system replacements, allowing them to modernize without shutting down production. The big takeaway? You don't need to rip and replace everything at once—smart upgrades can bridge the gap and make the transition smoother.
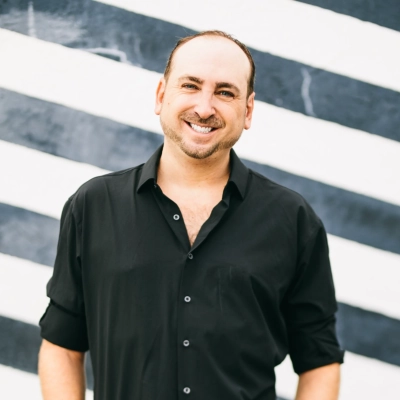
Prioritize Data Security
Modern businesses must prioritize data security when implementing Industry 4.0 technologies. With the increasing amount of data being collected, companies face the challenge of protecting sensitive information from cyber threats. This is especially important in industries that handle personal or financial data. Failing to secure data can lead to costly breaches and a loss of trust among customers.
Investing in robust security measures and staying updated on the latest threats is essential. Companies must not only protect their own data but also ensure the safety of their clients' information. Strengthening data security should be a top agenda for organizations embracing Industry 4.0 technologies.
Train Workforce for New Technologies
Educating and training the workforce is critical when adopting Industry 4.0 technologies. Many employees may not have the necessary skills to operate new machinery or software. By providing comprehensive training programs, businesses can ensure that their staff are up to date with the latest advancements. Additionally, skilled workers are more likely to contribute to the company's success.
Fostering an environment of continuous learning can lead to increased innovation and efficiency. Companies need to invest in upskilling their employees regularly. Make workforce development a central part of the transition to new technologies.
Manage Costs for Industry 4.0
Implementing Industry 4.0 technologies often comes with significant costs. The initial investment in advanced machinery, software, and training can be quite high. However, these upfront costs can lead to long-term savings through improved efficiency and productivity. Companies may also face ongoing expenses related to system maintenance and upgrades.
These costs can be a barrier for small and medium-sized businesses with limited budgets. To maximize the benefits, it's essential to carefully plan and allocate funds wisely. Businesses should prioritize budget management to ensure a smooth transition to Industry 4.0.
Address Interoperability Issues
Interoperability issues are a common hurdle when integrating Industry 4.0 technologies. Different systems and devices from various vendors may not always work seamlessly together. This can create disruptions and inefficiencies in operations. Ensuring that all technologies can communicate effectively is crucial for smooth implementation.
Companies often need to invest in additional tools or custom solutions to bridge these gaps. Addressing interoperability challenges is key to maximizing the benefits of new technologies. Businesses should focus on creating a cohesive technological ecosystem.
Monitor ROI for Industry 4.0
The return on investment (ROI) for Industry 4.0 technologies can be slow to materialize. While these technologies offer significant potential for long-term gains, seeing immediate benefits is uncommon. Patience and a strategic approach are vital for managing expectations. Companies must carefully monitor and evaluate the performance of new systems over time.
This evaluation helps in making informed decisions about future investments. It's important to set realistic goals and timelines for achieving ROI. Companies should adopt a long-term perspective to fully reap the rewards of Industry 4.0 technologies.