6 Steps for Creating a Safer Manufacturing Work Environment
In the high-stakes world of manufacturing, ensuring a safe work environment is paramount. Plant Operations Managers and Safety Coordinators share their valuable insights on this critical issue. The article begins with the importance of developing a proactive safety culture and concludes with the necessity of conducting regular risk assessments, encompassing a total of six expert recommendations. Discover actionable strategies to enhance safety measures within manufacturing facilities.
- Develop a Proactive Safety Culture
- Implement Robust Safety Protocols
- Invest in Advanced Safety Technologies
- Provide Comprehensive Safety Training
- Foster a Culture of Safety Awareness
- Conduct Regular Risk Assessments
Develop a Proactive Safety Culture
As a plant manager, one of the most critical steps I've implemented to enhance workplace safety is developing a comprehensive, proactive safety culture that prioritizes employee training and continuous risk assessment. We instituted a mandatory monthly safety workshop where all team members, from entry-level operators to senior management, participate in detailed safety protocol reviews and practical training scenarios. Our approach emphasizes not just compliance, but a genuine commitment to creating an environment where every employee feels empowered to identify and address potential hazards before they become incidents. We've integrated advanced safety technologies, including real-time monitoring systems and predictive analytics, to proactively detect potential workplace risks and implement preventative measures. Cross-departmental safety committees meet regularly to review incident reports, share best practices, and develop innovative safety strategies that go beyond standard regulatory requirements. I always advise other manufacturing leaders to invest in robust safety education, foster a culture of transparency and open communication about potential risks, and demonstrate leadership's unwavering commitment to employee well-being through consistent actions and resources. Technology and training are essential, but the most critical element is creating a workplace culture where safety is not a checklist, but a shared value embraced by every team member. Remember that effective safety management is an ongoing process of learning, adapting, and continuously improving, with the ultimate goal of protecting our most valuable asset: our employees.
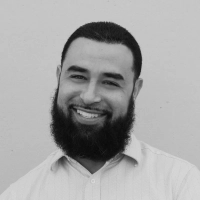
Implement Robust Safety Protocols
Implementing robust safety protocols and procedures is essential in manufacturing. These measures help set clear guidelines for safe operations. They also establish a foundation for regulatory compliance. By having strong protocols, potential accidents can be minimized.
Such actions show a commitment to employee safety. It is critical to regularly update these protocols. Encourage your team to follow these procedures consistently.
Invest in Advanced Safety Technologies
Investing in advanced safety technologies and equipment can significantly reduce workplace injuries. Modern technologies offer better protection and can foresee potential dangers. For example, machine guards and sensors can detect anomalies before they escalate. Equipping workers with the latest safety gear ensures they are protected.
Advanced technologies make the work environment safer for everyone. Companies should allocate resources to upgrade their safety measures. Act now to incorporate these technologies.
Provide Comprehensive Safety Training
Providing comprehensive safety training for all employees is crucial. Training ensures that everyone understands the potential risks in their workplace. It also equips them with the knowledge to handle emergency situations effectively. Well-informed employees can prevent accidents.
In addition, regular training sessions keep safety practices fresh in mind. This results in a more secure work environment. Promote continuous learning and safety training.
Foster a Culture of Safety Awareness
Fostering a culture of safety awareness and accountability encourages employees to take responsibility for their actions. When workers are aware of the consequences of negligence, they are more likely to adhere to safety practices. Building this culture needs consistent effort from management and employees alike.
It creates an environment where safety is everyone's priority. Over time, this leads to fewer accidents and a more committed workforce. Encourage everyone to participate in safety initiatives.
Conduct Regular Risk Assessments
Conducting regular risk assessments and identifying hazards helps keep the workplace safe. These assessments uncover potential risks that might be overlooked. By identifying hazards early, preventive measures can be implemented. Regular reviews ensure that no new risks have developed.
This proactive approach saves lives and reduces injuries. Make risk assessments a regular part of your safety strategy. Commit to conducting them frequently.