6 Programs for Fostering a Culture of Continuous Improvement in Manufacturing
In the quest for excellence in manufacturing, the integration of continuous improvement programs is pivotal. This article delves into cutting-edge strategies that have been vetted by industry experts to empower teams and streamline operations. Explore how innovative platforms, effective communication, and dedicated training can transform the shop floor into a hub of progress.
- Empower Teams with Digital Maintenance Platform
- Implement Daily Improvement Huddles on Shop Floor
- Establish Continuous Improvement Feedback Loops
- Launch Lean Training and Recognition Program
- Host Weekly 'Brew & Review' Sessions
- Prioritize Transparency in Organizational Communication
Empower Teams with Digital Maintenance Platform
At Mad Mexican, we foster a culture of continuous improvement by empowering our team with structured processes and clear performance metrics. Most importantly, we allow our team to set their own metrics based on production data, giving them ownership of their performance.
One key initiative we've recently implemented is the MaintainX Digital Maintenance Platform in our production facility.
By transitioning from manual maintenance tracking to a real-time digital system, our team now has instant access to daily performance metrics, helping them assess their progress in real time. Since they no longer need to spend time manually tracking data, technicians can focus more on machinery rather than paperwork. With a single click, they can access necessary tools and spare parts in advance, improving preventive maintenance, reducing downtime, and improving overall equipment efficiency.
The platform also enables production leaders to log work orders instantly, track recurring maintenance tasks, and ensure accountability, as they must approve work orders upon completion.
This initiative has not only streamlined maintenance operations but has also strengthened collaboration between different production stations and the maintenance team—reinforcing the belief that small, continuous improvements drive long-term success.

Implement Daily Improvement Huddles on Shop Floor
Creating a culture of accountability for continuous improvement in manufacturing starts with empowering employees to own both their processes and outcomes. One of the most successful strategies I've implemented is establishing daily improvement huddles on the shop floor.
These short, focused meetings bring teams together at the start of each shift to review performance metrics, identify bottlenecks, and discuss improvement opportunities. Here's how it works:
1. Visible Metrics: Key performance indicators (KPIs) like production targets, quality levels, and downtime are displayed on digital dashboards or boards visible to everyone. This transparency ensures every team member understands the goals and their role in achieving them.
2. Employee-Led Problem Solving: Each huddle includes time for employees to present ideas for resolving issues or improving processes. Instead of relying solely on management, workers take ownership of identifying and testing solutions. This shifts the culture from reactive to proactive and ensures continuous improvement is part of their daily routine.
3. Recognition and Feedback: Improvements are celebrated in real-time, whether it's reducing scrap, increasing throughput, or implementing a new safety practice. Recognizing individual contributions reinforces accountability and motivates others to participate.
This strategy fosters a shared sense of ownership and creates a cycle of small, incremental gains that add up to significant results. For example, after implementing this approach, one plant reduced downtime by 15% in three months, driven entirely by employee-initiated process enhancements. The key is making improvement part of everyone's day-to-day work—not just a one-time initiative—while providing the structure and recognition to sustain accountability over the long term.

Establish Continuous Improvement Feedback Loops
Fostering a Culture of Continuous Improvement
Cultivating a culture of continuous improvement within an organization, department, or team can be a challenging and ongoing endeavor. However, the rewards are well worth the effort, leading to substantial opportunities and positive change. If not managed effectively, it can result in chaos and confusion.
The Pitfalls of Unmanaged Change
When teams perceive constant change as fleeting or refuse to accept it, waiting for the next change, it becomes counterproductive. This highlights the need for a thoughtful approach to continuous improvement.
Successful Strategies
1. Leverage Team Feedback and Engagement: Encourage team members to share their thoughts and ideas, fostering a sense of ownership and engagement.
2. Embrace a Growth Mindset: Communicate that nothing is set in stone, and improvements are ongoing.
3. Post-Change Feedback and Evaluation: Hold meetings to gather feedback and identify areas for further improvement.
4. Empower Team Members: Encourage and reward individuals who bring new ideas and solutions, promoting a grassroots approach to improvement.
5. Continuous Improvement Loops: Establish a regular cycle of feedback, evaluation, and implementation to sustain momentum.
By implementing these strategies, organizations can create a culture of continuous improvement, where change is embraced as a collective effort, a business differentiator, driving sustainable growth and success.

Launch Lean Training and Recognition Program
Creating a culture of continuous improvement within manufacturing operations requires strategic efforts, one of which is the implementation of Lean manufacturing principles. At our facility, we launched a Lean training program that educates employees at all levels about waste reduction, continuous flow, and the importance of efficient processes. Through regular workshops and hands-on projects, staff members learn how to identify inefficiencies in their daily work and propose practical solutions. This engagement not only boosts productivity but also empowers employees, fostering a sense of ownership and accountability.
To further embed these practices, we established a recognition system to celebrate teams and individuals who successfully implement significant improvements. This system not only motivates staff but also sets a benchmark for excellence within the organization. By focusing on training, participation, and recognition, we've observed marked improvements in our operational efficiency and a stronger alignment with our overall business objectives. Encouraging continuous improvement is not just about introducing new processes; it's about nurturing an environment where every employee feels valued and capable of influencing positive change.
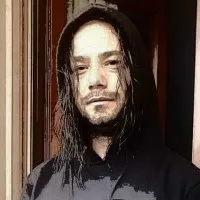
Host Weekly 'Brew & Review' Sessions
One of the ways we've created a culture of ongoing improvement in our production processes at Cafely is by having a weekly "Brew & Review" session on the production floor. It's a casual but intentional sit-down where our packaging and logistics team has the opportunity to provide feedback on what's going well, what's not, and where we can do better—even minor things like labeling workflow or rearranging the order of sealing and boxing. One of the suggestions for streamlining how we stage our instant coffee sachets for bulk orders actually reduced packing time by almost 10%. Providing our team with a regular, judgment-free space to share their opinions has not only made us more efficient but has also created genuine ownership in the process. Everyone feels like they have a stake in the game.

Prioritize Transparency in Organizational Communication
One key initiative I've implemented to foster a culture of continuous improvement and employee engagement is transparency and communication. I truly believe that creating an environment where everyone feels informed and involved is essential to maintaining motivation and connection. To achieve this, I make it a priority to regularly share organizational goals, successes, and challenges with my team. This transparency ensures that everyone is on the same page and understands not just where we're headed, but how they contribute to the journey.
By being open about the goals and obstacles we face, I help my team feel like active participants in the process. It's important to me that they understand the bigger picture and how their individual contributions align with our overall mission. I hold regular meetings, use email updates, and other communication channels to keep everyone informed. This consistent sharing builds trust, as they know they're receiving clear, up-to-date information.
When challenges arise, I share those openly as well, encouraging everyone to contribute their ideas and solutions. By creating a space for open dialogue, I empower my team to think creatively and work collaboratively toward solutions. This not only fosters engagement but also drives innovation. Furthermore, I make sure to celebrate our successes, big and small, to reinforce that we are all in this together, continuously moving forward.
By maintaining open communication and transparency, I've found that my team becomes more engaged, motivated, and invested in both their personal growth and the collective success. This environment of trust and inclusion is a vital part of creating a culture where continuous improvement is not just encouraged, but woven into the fabric of our work.
