6 Methods to Manage Lead Times Effectively in Manufacturing
In today's fast-paced manufacturing landscape, managing lead times effectively can make or break a company's success. Businesses are constantly seeking innovative strategies to streamline their operations and stay ahead of the competition. This article explores several powerful methods that can help manufacturers optimize their lead times, boost efficiency, and ultimately enhance their bottom line.
- Implement Demand Forecasting and Buffer Stock
- Adopt Just-In-Time Inventory Management
- Utilize Advanced Production Scheduling Algorithms
- Foster Strategic Supplier Partnerships
- Deploy Real-Time Supply Chain Tracking
- Invest in Flexible Manufacturing Technologies
Implement Demand Forecasting and Buffer Stock
To effectively manage lead times in my manufacturing business, I implemented a demand forecasting system that combines historical sales data with real-time market trends. One successful strategy has been setting up buffer stock for high-volume or long-lead components, which helps absorb delays without halting production. I also built stronger relationships with key suppliers, including negotiating priority terms for urgent orders. This combination of data-driven planning and proactive supply chain communication has significantly reduced backorders and customer wait times. As a result, we've improved on-time delivery rates and built greater trust with our clients.
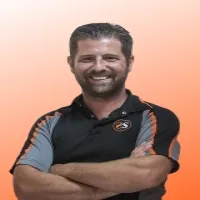
Adopt Just-In-Time Inventory Management
Implementing just-in-time inventory management systems can greatly improve lead times in manufacturing. This approach focuses on reducing waste by only ordering and holding the inventory needed for immediate production. By aligning inventory levels with actual demand, companies can minimize storage costs and reduce the risk of obsolete stock.
Just-in-time systems require close coordination with suppliers and accurate demand forecasting. When implemented correctly, this method can lead to significant reductions in lead times and improved overall efficiency. Manufacturing companies should consider adopting just-in-time inventory management to streamline their operations and boost productivity.
Utilize Advanced Production Scheduling Algorithms
Advanced algorithms can revolutionize production scheduling and effectively manage lead times. These sophisticated tools analyze various factors such as machine capacity, order priorities, and resource availability to create optimal production schedules. By minimizing idle time and maximizing resource utilization, these algorithms help manufacturers meet deadlines more consistently.
The use of such technology can also adapt quickly to changes in demand or unexpected disruptions. Implementing advanced scheduling algorithms often results in smoother production flow and reduced lead times. Manufacturers should explore the benefits of integrating these powerful tools into their operations to gain a competitive edge.
Foster Strategic Supplier Partnerships
Establishing strategic partnerships with key suppliers is a crucial method for managing lead times in manufacturing. By fostering close relationships with suppliers, companies can ensure more reliable and timely deliveries of raw materials and components. These partnerships often involve sharing forecasts, collaborating on product development, and implementing joint quality improvement initiatives.
Such close cooperation can lead to reduced lead times, improved product quality, and increased flexibility in responding to market changes. Strong supplier partnerships can also result in preferential treatment during times of scarcity or high demand. Manufacturers should prioritize building and nurturing these strategic relationships to enhance their supply chain efficiency.
Deploy Real-Time Supply Chain Tracking
Real-time tracking systems provide invaluable supply chain visibility, which is essential for effective lead time management. These systems use technologies such as GPS, RFID, and IoT sensors to monitor the movement of materials and products throughout the supply chain. With up-to-the-minute information, manufacturers can quickly identify and address potential delays or bottlenecks.
Real-time tracking also enables more accurate delivery estimates and proactive problem-solving. This increased visibility can lead to significant reductions in lead times and improvements in customer satisfaction. Companies should invest in implementing robust real-time tracking solutions to gain better control over their supply chains.
Invest in Flexible Manufacturing Technologies
Investing in flexible manufacturing technologies is a forward-thinking approach to managing lead times effectively. These technologies, such as modular production lines and multi-purpose machinery, allow manufacturers to quickly adapt to changing product requirements or demand fluctuations. Flexible manufacturing systems can reduce setup times, minimize production changeovers, and enable smaller batch sizes without sacrificing efficiency.
This adaptability often translates into shorter lead times and improved responsiveness to customer needs. Additionally, flexible technologies can help manufacturers maintain competitiveness in rapidly evolving markets. Forward-thinking companies should consider incorporating flexible manufacturing technologies into their production strategies to stay ahead of the curve.