6 Lessons Learned for Optimizing Production Efficiency in Manufacturing
Maximizing production efficiency is a multifaceted challenge in the manufacturing sector. This post delves into proven strategies, from leveraging real-time data to embracing automation, that can streamline operations and cut costs. Discover how these initiatives not only enhance productivity but also empower a skilled workforce.
- Use Real-Time Data for Decision-Making
- Embrace Automation for Consistent Output
- Minimize Waste to Lower Costs
- Streamline Workflows to Boost Productivity
- Prioritize Preventative Maintenance
- Upskill Workforce for Better Efficiency
Use Real-Time Data for Decision-Making
One of the most valuable lessons I've learned about optimizing production efficiency is the importance of leveraging real-time data to drive decision-making. Implementing tools like Manufacturing Execution Systems (MES) or IoT-enabled sensors on production lines has been a game-changer. These tools provide actionable insights into downtime, cycle times, and bottlenecks. For instance, in our facility, we identified a persistent bottleneck in the packaging line through time studies and data analysis. By implementing Line Balancing, adjusting shift schedules and balancing workloads, we reduced downtime by 15% and improved throughput. The key tip- Don't rely solely on intuition-use data to uncover inefficiencies and make targeted improvements.
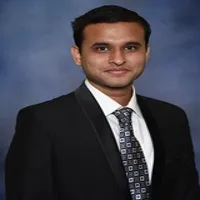
Embrace Automation for Consistent Output
Automation is a vital element in optimizing production efficiency within manufacturing. It allows for consistent, high-quality output while reducing the potential for human error. Additionally, automation can work around the clock without fatigue, boosting overall productivity.
Investing in the right technology can streamline operations and cut down on long-term costs. For any manufacturing business aiming to stay competitive, it is essential to embrace automation and adapt to new advances in the field. Don't wait; start integrating automation today.
Minimize Waste to Lower Costs
A crucial lesson in optimizing production efficiency is the importance of minimizing waste. This practice not only helps in lowering costs but also in protecting the environment. By cutting down on excess material use, manufacturers can save money and resources.
Efficient waste management also includes recycling and reusing viable materials. By focusing on waste reduction, companies can enhance their bottom line and contribute to a more sustainable future. Take steps now to minimize waste in your production processes.
Streamline Workflows to Boost Productivity
Streamlining workflows is fundamental in enhancing production efficiency in manufacturing. By analyzing current processes and removing unnecessary steps, manufacturers can significantly boost productivity. A clear, well-structured workflow ensures that everyone knows their role and responsibilities, reducing confusion and delays.
Additionally, streamlined processes lead to quicker turnaround times, which can satisfy customer demands better. Make the effort to streamline your workflows and see the benefits unfold.
Prioritize Preventative Maintenance
Preventative maintenance is key to keeping production lines running efficiently and avoiding costly downtime. Regular checks and upkeep can identify potential issues before they become major problems. This proactive approach helps in extending the lifespan of machinery and maintaining consistent quality in production.
It also means fewer disruptions to the workflow, allowing more products to be completed on schedule. Start prioritizing preventative maintenance to keep your production line at peak performance.
Upskill Workforce for Better Efficiency
Upskilling the workforce is an essential strategy for optimizing production efficiency in manufacturing. Well-trained employees can operate machinery more effectively and adapt to new technologies seamlessly. This not only improves productivity but also fosters a culture of continuous learning and improvement.
Skilled workers are better equipped to troubleshoot problems and implement solutions quickly. Invest in training programs to upskill your workforce and drive your manufacturing success.